What Makes Aluminum Welding Wire ER5356 Ideal For Lightweight Structures
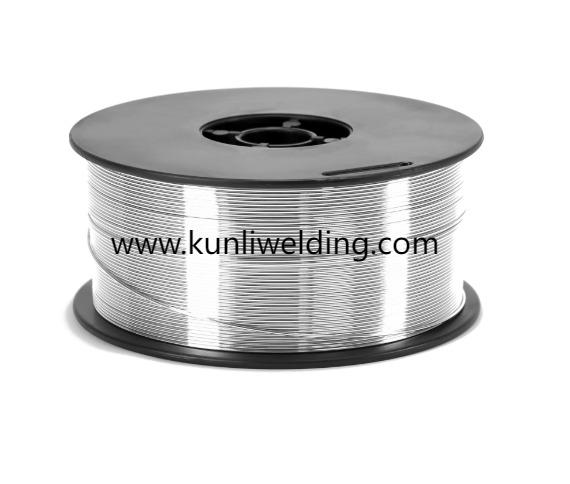
In modern fabrication settings where joining aluminum components demands both strength and flexibility, Aluminum Welding Wire ER5356 has established itself as a versatile choice for demanding applications. From architectural façades to high performance transport frames, this filler metal offers a balance of mechanical resilience and corrosion resistance that aligns with recent industry shifts toward lightweight structures and sustainable materials. By understanding its unique properties, engineers can make informed selections that enhance weld integrity and streamline production workflows.
This alloy's composition features magnesium as its primary strengthening element, delivering improved tensile characteristics compared to pure aluminum filler. Such enhancement supports loadbearing welds in structures exposed to cyclic stresses and dynamic loading. At the same time, its moderate alloying profile promotes good weld pool fluidity, allowing operators to achieve smooth bead contours on both flat and vertical surfaces. These qualities have captured attention as manufacturers embrace electric vehicle platforms and renewable energy frameworks that rely on durable yet lightweight assemblies.
Weldability is a standout feature of this wire grade. Compatibility with common welding processes ensures that both manual and robotic MIG systems can utilize the same feedstock without extensive parameter recalibration. Automated lines benefit from consistent melting behavior, reducing interruptions due to wire burn back or stick slip. In manual workshops, technicians appreciate the wire's predictable arc stability, which helps maintain seamless travel speeds and uniform penetration even when tackling complex joint geometries.
Resistance to environmental corrosion further widens its application scope. In marine and coastal installations where salt spray accelerates material degradation, this filler metal forms protective oxides that delay pitting and stress corrosion cracking. Infrastructure projects such as pedestrian bridges and offshore platforms leverage these properties to extend maintenance intervals and uphold safety standards. As news about coastal resilience initiatives gains momentum, this corrosion performance has become an asset in procurement conversations.
Surface preparation and parameter tuning play vital roles in unlocking optimal performance. Cleaning joint edges to remove oxide films enhances fusion, while adjusting voltage and wire feed speed tailors heat input for thin or thick sections alike. When following recommended travel angles and contact tip selections, operators produce welds that require minimal grinding or reshaping. This efficiency supports lean manufacturing goals and helps fabricators meet ambitious project timelines without compromising on quality.
Quality assurance practices integrate seamlessly with digital inspection tools. High resolution cameras and ultrasonic scanners verify bead geometry and detect subsurface flaws, providing immediate feedback on weld soundness. Traceability systems tag each spool with batch identifiers, linking material certificates to production records. Such transparency not only builds customer confidence but also simplifies compliance with evolving safety regulations in sectors like public transit and chemical processing.
Maintenance teams benefit from its low spatter tendency. Reduced spatter means fewer postweld cleanup tasks and less abrasive dust in the workplace. This contributes to a healthier environment and reduces the burden on extraction systems. For shops balancing throughput with occupational safety goals, these ergonomics make a noticeable difference in daily operations.
Training programs that cover joint design, parameter selection, and defect prevention accelerate skill development among welders. Handson workshops led by experienced instructors demonstrate fusion techniques across typical base metal thicknesses. Virtual reality simulators offer additional practice in a riskfree setting, helping operators refine handeye coordination before tackling live welds. By investing in both material knowledge and practical skills, teams achieve higher firstpass success rates and lower scrap costs.
Global supply chains ensure that this wire grade remains readily available. Strategic stock locations feed regional distribution centers, guaranteeing timely deliveries even when demand surges. Consistent inventory tracking tools enable procurement managers to place orders at the optimal time, avoiding production pauses and inventory overstock. This logistical reliability supports uninterrupted workflows in high volume manufacturing environments.
Whether fabricating architectural features, electric vehicle frames, or coastal structures, selecting the right filler metal is critical. Its blend of mechanical strength, weldability, and corrosion resistance positions it as a go to solution for a wide range of projects. To explore detailed specifications, technical support services, and purchasing options, visit www.kunliwelding.com/product/ .
- Art
- Causes
- Crafts
- Dance
- Drinks
- Film
- Fitness
- Food
- Games
- Gardening
- Health
- Home
- Literature
- Music
- Networking
- Other
- Party
- Religion
- Shopping
- Sports
- Theater
- Wellness